The structure accommodated a permanent, self-cleaning belt magnet system on an existing stacker conveyor. To facilitate transport and installation, we designed the structure as bolted rather than fully welded.
The conveyor magnet structure was mounted on four concrete footings and secured with chemical anchors. The structure was equipped with a chute that directed the tramp metal to a forklift-removable bin. As part of the design process, we ensured that it complied with all the relevant Australian standards i.e. AS4100 and AS1170 (wind loading).
This magnet system suspended an electro- or permanent magnet above a conveyor belt and extracted tramp metal from the ore. As a result, it provided protection to downstream equipment. In most cases, a conveyor might already have a magnet installed at the head end of the conveyor. However, for various reasons, this might have been omitted. To rectify this, a belt magnet could be installed at the head end of the conveyor, which was the preferred option. However, this solution might not be always possible. In some cases, the head end was not able to accommodate the higher loads from the magnet. Also in other cases, the limited access at the head end of the conveyor would be unfavorable. In this case, our client opted to install the structure on a lower part of the conveyor where it could be supported from ground level.
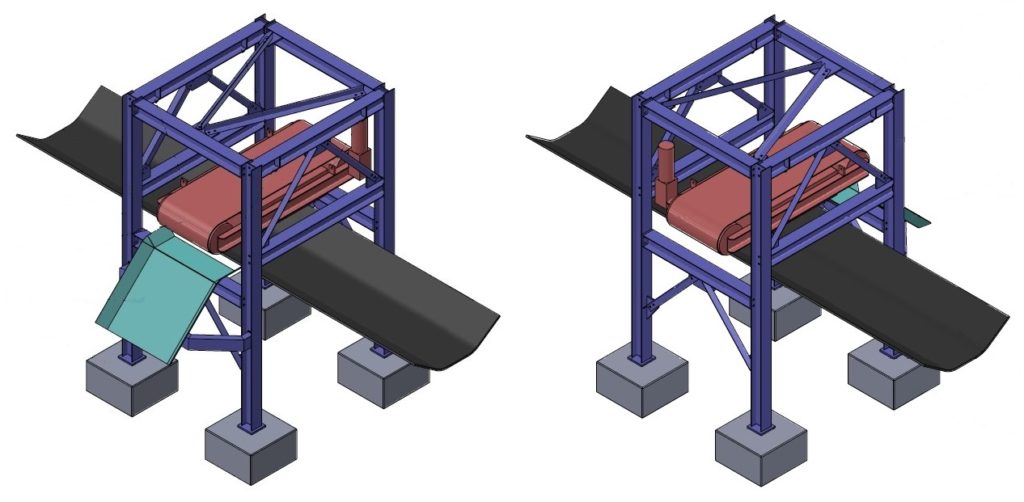
Do you have a similar application? Give the team at Dynamic Engineering a call today or send us and e-mail. We have the ability to design and draw your new structure (including shop drawings) to your exact requirements, whilst remaining compliant to the relevant Australian Standards.